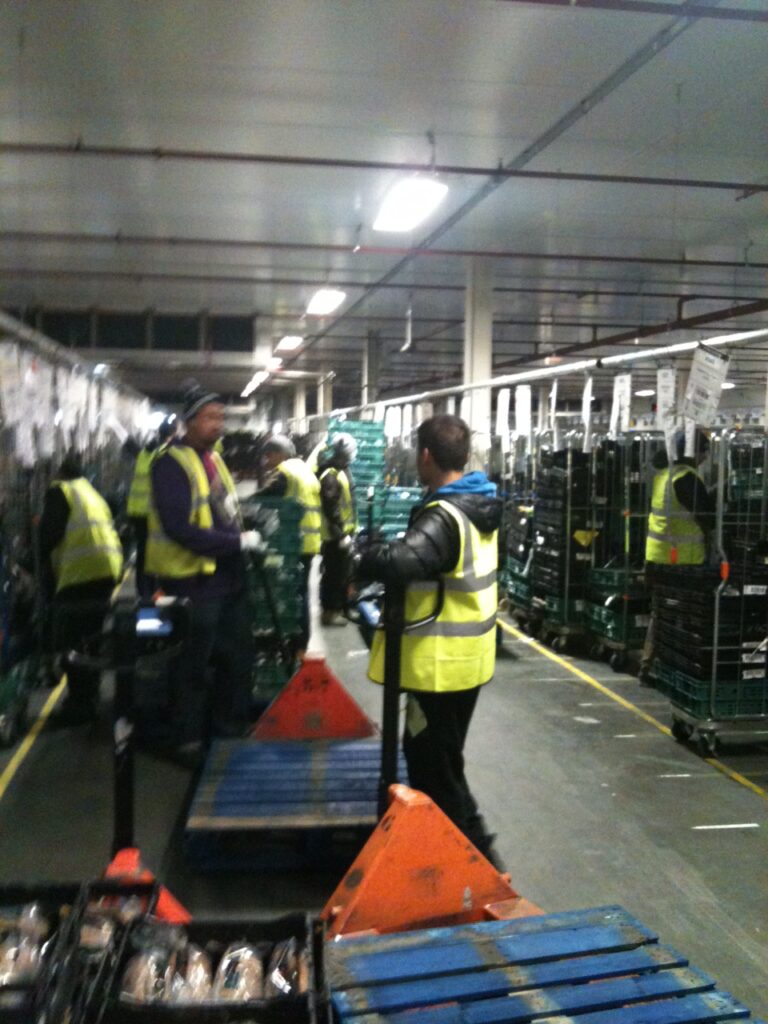
In 2015 we met in the Sainsburys chill-house (this refers to the temperature, folks!) in Greenford, picking salted butter and egg-cress sandwiches for 143 supermarket outlets in the London area while being bombarded with Radio Heart non-stop. There were Nepali Olympic gymnasts, Polish hooligans (and of course the one and only Polish rasta, just imagine his accent!), Sudanese lawyers, Afghani child refugees and Kurdish primary school teachers with us. As temp workers who were paid only 70% of the permanent workers’ wages, while having to work double as hard, we organised a slow-down with mixed results. Eight years later a friend of ours felt nostalgic and went back to the Sibirian chill. You can read his report below – if you get hooked you can read more in our free version of ‘Class Power on Zero-Hours’…
I want to share my experience working for Wincanton-Sainsburys at Greenford site, in the period between March till September 2023. Wincanton is a logistics contractor that takes care of the supply chain for Sainsburys and Waitrose, in my case performing picking duties. I started to work doing the night shift in the ambient department from 20:00 till 6:00, 4 days on, 4 days off as a shift pattern with 45 minutes paid breaks that I found a positive point. In my previous period I only worked in the chill-produce chambers, so for my ambient chamber was a new experience. Last time I worked through an agency named ‘Templine’, this time I was contracted directly by Wincanton.
I was told that Templine disappeared in 2019, another agency named ‘Mack’ was hired until 2021, now an agency named ‘Siamo’ is providing agency workers. ‘Siamo’ is a re-branded ‘Templine’, but none of the former Templine colleagues was still working at Wincanton. Neither management, administrative or shop-floor workers. Another detail that I would like to remark on is the background of the workforce. Years ago there were a lot of workers from Poland, Romania, Hungary or Lithuania. Now there are only a few workers from Poland left, all of them working directly with Wincanton. With the agency the vast majority are from Indian background, especially from Goa. This is a big change from my previous period.
Another big change is that now the temp-workers earned the same as the permanent workers! Eight years ago there was a major gap of 30 to 40%.
The picking was performed using a voice-picking device and LLOP truck (Low-level order picker), the voice device wasn’t working very well, every day at some point the device didn’t recognize voice commands properly or it was slow, affecting performance. I asked my colleagues if they had the same issues and they confirmed. In fact most of the colleagues were using hand-held visual scanners, rather than the voice-picking device. After 4 weeks I suggested to use the hand-held scanner and I was allowed to use it, but in the following week the shift managers told me that higher management didn’t allow me to use the hand-held scanner while on probation. In my case there was a big improvement with the hand-held scanners.
The working conditions were correct, the grids were not too crowded. The issue was the pick rate, which was 184 picks per hour, which I found high. The products ranged from light packs of crisps, sweets boxes or sauces to the most demanding items like packs of water, beers, soft-drinks and bottles of wine. During the first three months, I was on probation. To pass probation you need to meet 90% of the pick rate (184 picks per hour), no more than 2 periods of absence for sickness. I struggled to meet the pick rate, which was between 65 and 76 percent. I had frequent issues with the voice device, when I was allowed to use the hand-held scanner my picking rate improved to 84 percent. After the 3 months probation I didn’t meet the targets required, but because I worked in the past in the chill chamber management decided to extend my probation by another 3 months, but this time in the chill chamber, where only hand-held scanners are used.
The chill chamber is a controlled temperature chamber, between 2-3 degrees and the products to pick were meat, ready meals, sauces, and dairy products. The chamber was basically the same as before, but this time there were 3 grids instead of 4. The work atmosphere was more chaotic than ambient and congestion on the grids were common, especially at the start of the shifts when the trucks passed through, not in very safely manner, to drop pallets. Nothing had changed, neither the rat race with the same “tricks” to increase the pick rate, to meet the targets that otherwise were extremely difficult to archive. I was running up and down, throwing the stuff into the cages. In ambient it was not like that. The pick rate was 210 items per hour, which I found very demanding if not unrealistic.
I had probation reviews every two weeks, in the chill/produce chambers my pick rate increased significantly to 86 percent. I was told by my probation manager that if in the next two weeks I managed to increase performance to 90 percent I would pass my probation. Every day by the end of the shift I was checking my performance, and many of the days I was above 95 percent. On a couple of occasions even over 100 percent. To my surprise, after two weeks the manager showed me my pick rate statistics, which said that I was at 87 percent. I challenged the data and I insisted that many days I was well above the percentage she was showing me. After a while of discussing the issue she only told me that the system was ‘adjusting the rates hourly’, without any other explanation. She told me that I have another two weeks to archive the pick rate of 90 percent. I felt more than disappointment, I would say I was outraged. I had the feeling that I was pushed to perform more than 100 percent. In the following weeks I didn’t work as hard as I used to, because I thought it was pointless and I started to look for another job. I found one, so there is more to come.
I hope you find this report interesting.